Unlock the power of Factory 4.0
- Home
- TechTrends
- Unlock the power of Factory 4.0

Today’s factories must be more flexible, more communicative and more efficient, while still serving people.
With the Smart Factory 4.0 program, ALTEN is exploring all the fundamental topics of Industry 4.0 focused on the transformation of industrial sites. The technologies deployed are integrated with each other to provide more efficient production from an economic, ecological, and human perspective.
Human at the heart of Industry 4.0
In an increasingly digitalised world, ALTEN’s offer is designed to put technology at the service of humans. Our approach encompasses various strategies tailored to address the needs & requirements of businesses, by placing humans at the heart of the equation:
- Manage production in real-time: through convergence of IT and OT networks
- Increase efficiency and productivity: assistance by generative AI
- Ensuring safety: predict accidents & anticipate real and virtual risks
- Optimise risk management: whether logistical, manufacturing or quality related
- Facilitating handling: robotization & optimization of productions flows
- Optimising resources & waste: to reach zero or positive environmental impact
- Optimising quality: products & services
- Improving knowledge & training: through assistance during operations & support in continuous learning
ALTEN’S 4.0 TECHNOLOGY BRICKS
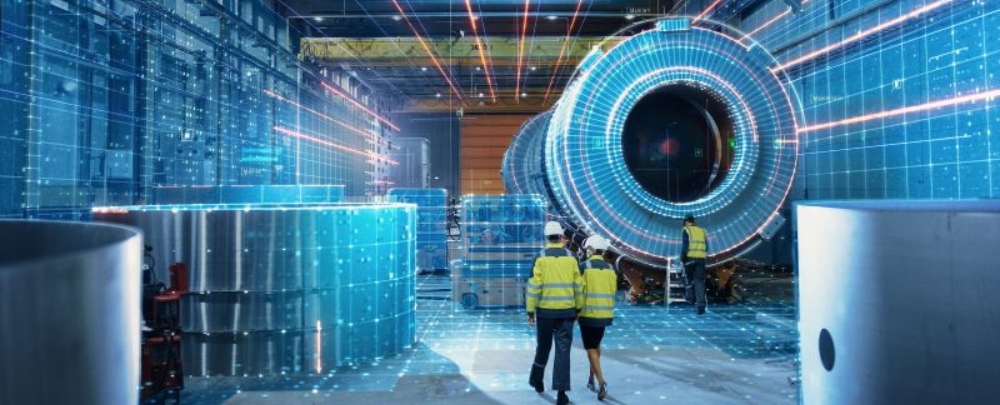
- Optimisation of the IT/OT connection for real-time update of the Digital Twin
- Automating Data & images processing and preparation with AI in the Edge and Cloud
- Integration of smart IoT sensors for data processing close to the machines
- Use of 3D printing for the creation and integration of “smart parts”

- Implementation of real-time control of machines and factory
- Implementation of Machine Learning in the Factory
- Interaction of the Intelligent Hypervisor with its users

- Implementation of mixed reality solutions to assist operators
- Generative AI to ease human-digital interactions
- Life cycle assessment and energy performance
Our Success Stories
Reliable connectivity is a core necessity for the plants of the future, to guarantee high levels of security, throughput, and availability. Private 5G network provides high-speed and high volume of communication but also network slicing type functionalities to manage critical flows:
- Quality of Services (QoS) control through bandwidth reservation & definition of classes of service adapted to each type of flow
- Security control through :
- Enhanced security compared to 4G/Wifi networks
- Segmentation into sub-networks with specific rules per flow
Finally, 5G brings a multi-service network with controlled OPEX and without billing to the SIM.
ALTEN has partnered with Bouygues Telecom Entreprises & SIEMENS to accelerate the development of 5G for Industry 4.0.
To demonstrate the endless possibilities of Smart Factory 4.0 innovation, the ALTEN Innovation teams have built a real drone assembly plant combined with a Digital Twin. This “Mini Plant 4.0”, can be used to analyse the impact of the plant’s various intelligences on industrial processes and efficiency.
It can be remotely controlled in virtual reality. Thanks to machine learning algorithms, it is possible to monitor and process large quantities of data collected from sensors, enabling alerts to be created for any deviations detected in real time (on-board AI), controlled time (plant AI in Edge Computing) and deferred time (company AI in Cloud Computing). This helps to prevent production problems and reduce the risk of accidents by supporting human decision-making, forecasting performance indicators and simulating results.
Artificial intelligence (AI) and machine learning provide information on performance optimisation, maintenance, emissions and efficiency.
ALTEN partners with STMicroelectronics to develop Smart IoT deployment on a large scale. These embedded systems perform automated missions, give contextualized alerts, and provide high added-value services.
One use case is the support of a major aircraft manufacturer in the usage of predictive and prescriptive maintenance. The implementation of a smart system, collecting data through STMicroelectronics intelligent sensors, has allowed to extend the life of cutting tools by up to 30%, drastically reducing costs.